Discover How Cotton is Made into Yarn: A Step-by-Step Guide
Cotton is one of the most commonly utilized natural fibers in the textile industry, and the process begins with the conversion of cotton fibers into yarn. Making cotton into yarn involves several essential steps that ultimately create the foundation for fabric production.
In this article, we’ll look at the cotton yarn manufacturing process, highlighting each step involved, from cultivation and harvesting to dyeing and finishing. By the end of this article, you’ll understand how cotton is made into yarn and its role in creating the fabrics we use every day.
“Delve into the intricate process of turning cotton into versatile yarn, and unravel the journey of jute as it transforms into crafting yarn.”
Key Takeaways:
- Making cotton into yarn involves several essential steps, from cultivation and harvesting to yarn finishing.
- Understanding how cotton is made into yarn is essential to appreciate its significant role in the textile industry.
Cultivation and Harvesting of Cotton
Cotton, a natural fiber, finds extensive use in creating fabrics, textiles, and clothing. Understanding how cotton is made into yarn is essential to appreciate the complexity and craftsmanship of producing high-quality fabrics. The journey from cotton to yarn involves several critical steps, including cultivation and harvesting, ginning and cleaning, carding and combing, spinning, ply and twist dyeing and finishing, and yarn manufacturing and distribution.
Before being transformed into yarn, cotton goes through a lengthy journey that starts with cultivation on farms worldwide. Cotton plants usually flourish in warm climates, necessitating abundant sunlight and water for optimal growth. Once the cotton bolls are fully grown, they are harvested through various methods, including mechanical picking or handpicking, depending on the type of cotton and the available resources.
After the cotton is harvested, it undergoes a thorough cleaning and removal of the seeds and impurities. This process is called ginning and is essential to produce high-quality cotton fiber. The cotton fibers are then carded and combed to remove any remaining impurities and align them in a parallel position, creating a web of cotton fibers that can be spun into yarn.
The spinning process involves drawing out the cotton fibers and twisting them together to create a long, continuous strand of yarn. This forms the foundation for fabric production and can undergo additional processing to increase its strength and durability through the ply and twist process. The yarn can be dyed and treated to introduce color and texture, and once this process is complete, it is prepared for manufacturing and distribution.
Growing and gathering cotton is vital in shaping the final product’s quality, durability, and overall appearance. From cotton to yarn, the journey is both fascinating and complex, and it requires a significant amount of skill and craftsmanship to produce high-quality cotton yarn that can be used in various industries.
Ginning and Cleaning the Cotton Fiber
After being harvested, cotton must be treated to remove its seeds and any impurities before it can be spun into yarn. This process is known as ginning and cleaning.
The first step is to separate the cotton fiber from the seed. This is done using a cotton gin, which combs through the cotton to remove the seeds. Once the seeds are removed, the cotton is referred to as lint.
The lint then goes through a cleaning process, which involves removing any remaining impurities, such as dirt, leaves, stems, and other debris. This process is crucial to ensure that the resulting yarn is high quality and free from unwanted contaminants.
Ginning and Cleaning Process | Description |
---|---|
Cotton Gin | A machine that separates cotton fibers from the seeds. |
Cleaning | The process of removing any remaining impurities from the cotton lint. |
The ginning and cleaning process is essential in preparing the cotton fiber for the next step: carding and combing.
Stay tuned for the next section to further explore the carding and combing process.
Carding and Combing the Fiber
Once the cotton fibers have been ginned and cleaned, they are carded and combed to align the fibers further, remove any remaining impurities, and prepare them for spinning into yarn.
Carding separates and straightens the cotton fibers by passing them between two rollers covered in wire teeth. The fibers are then drawn through a small opening to create a thin, flat sheet of cotton called a web. The web is then condensed and wound into a loose rope-like form called a sliver.
Combing is an optional process that refines the sliver by removing any short fibers or remaining impurities. This process involves passing the sliver through a series of combs with fine teeth, which align the fibers even more and create a smoother, more consistent sliver. The resulting sliver, a top, is ready to spin into yarn.
The carding and combing process is crucial in ensuring the quality and consistency of the cotton fiber, which ultimately determines the strength and appearance of the finished yarn and fabric. By removing any impurities and aligning the fibers, the cotton is better able to withstand the stress and tension of the spinning process, resulting in a more robust and more durable yarn.
Spinning the Cotton Fiber into Yarn
After the cotton fibers are carded and combed, they are ready to spin. Spinning is drawing out the fibers and twisting them together to form yarn. This is the final step in converting cotton into yarn, creating the foundation for fabric production.
The spinning process begins with a machine that pulls the cotton fibers through small metal teeth, aligning them uniformly. The fibers are then drawn out and twisted together to form a thin strand of cotton yarn. This process is repeated until the desired thickness and strength of the yarn are achieved.
Two main spinning techniques are used in cotton yarn manufacturing: ring and open-end spinning. The fibers are drawn out and twisted in a ring, spinning using a rotating spindle and a ring, creating a solid and durable yarn. The fibers are drawn out and twisted together in open-end spinning, using a high-speed spinning rotor, producing a softer and more cost-effective yarn.
Once the cotton fibers have been spun into yarn, they are wound onto bobbins or cones to prepare for the next stage of the manufacturing process. The yarn can also be treated with finishes to enhance its appearance, texture, and performance.
Ply and Twist: Enhancing Yarn Strength
After the cotton fibers are carded and combed, they can spin into yarn. However, to ensure that the yarn is strong enough to withstand the rigors of use, it must first go through the ply and twist process.
This process involves twisting multiple strands of yarn together to create a stronger, sturdier yarn. The number of strands used and the direction of the twisting can vary, with some yarns being plied in one direction while others are plied in the opposite direction.
The yarn twist is also crucial in determining its strength and durability. Too little twist and the yarn may fall apart when used; too much twist and the yarn may become stiff or wiry. Achieving the perfect balance of twist is a carefully calibrated process, requiring skilled artisans to monitor the yarn as it is twisted and adjust the tension as needed.
Cotton yarn adequately plied and twisted is stronger and more durable than yarn that has not undergone this process. This is particularly important in textile manufacturing, where fabrics must withstand repeated use and washing.
Enhancing Yarn Appearance and Texture
In addition to increasing the strength of the yarn, the ply and twist process can also be used to enhance its appearance and texture. Yarn manufacturers can create yarns with unique and exciting visual effects by using different colors or textures in the twisting process.
They can also adjust the twist of the yarn to create different textures, from smooth and silky to rough and textured. This allows textile manufacturers to create fabrics with various looks and feels, from soft and cozy to crisp and structured.
The ply and twist process is crucial in cotton-to-yarn, ensuring the final product is strong, durable, and visually appealing. Without it, the cotton yarn would lack the strength and versatility necessary for use in the textile industry.
Yarn Dyeing and Finishing
After spinning, the cotton yarn is ready to be dyed and finished. Yarn dyeing is adding color to the yarn using different methods. It can be done at any stage of the yarn manufacturing process but is usually performed after spinning.
The dyeing process can be done through skein, package, and space dyeing. Skein dyeing is the most common method, where the yarn is wound into loops and then dyed. Package dyeing involves dyeing the yarn in the form of cones or spools, while space dyeing creates yarn with random and varying color patterns.
After dyeing, the cotton yarn goes through a finishing process to enhance its appearance, texture, and performance. Some standard finishes include sizing, which adds stiffness to the yarn, and mercerization, which increases its strength and luster. Additionally, the yarn may be treated with special coatings to make it flame-retardant, water-resistant, or wrinkle-free.
The final stage of yarn finishing is to wind and package the yarn. The length of cotton yarn can vary from thousands of yards to over a mile. Therefore, it must be wound onto bobbins, cones, or spools for easy handling and transportation. These packages are then labeled, boxed, and shipped to textile manufacturers, knitting mills, and other customers who use cotton yarn in their production process.
The cotton yarn manufacturing process is complex and involves multiple stages, each crucial in creating high-quality yarn. From cultivation and harvesting to spinning and finishing, every step needs to be done with precision and care to produce cotton yarn of the highest quality.
Yarn Manufacturing and Distribution
Once the cotton fibers have been spun into yarn, they are ready for the final stages of manufacturing and distribution. These processes ensure the cotton yarn is packaged and delivered to retailers and other end-users for further processing.
The first step in yarn manufacturing is winding the yarn onto spools or cones. This is typically done using a machine called a “winder,” which winds the yarn onto a spool or cone neatly and consistently. The spools or cones are then labeled and packaged for shipping.
Cotton yarn is distributed domestically and internationally, with many textile companies producing and shipping cotton yarn to various parts of the world. The demand for cotton yarn is high, with the textile industry relying heavily on cotton yarn to produce a wide range of fabrics and textiles. This includes everything from clothing and home textiles to industrial fabrics and medical textiles.
As cotton yarn is shipped worldwide, it goes through various distribution stages. This includes handling and storage at warehouses, truck, train, or ship transportation, and delivery to retailers and end-users. The cotton yarn is carefully monitored and tracked at each stage to ensure it reaches its destination on time and in the proper condition.
Cotton yarn production is intricate and demands meticulous attention to detail at every stage. From cultivation and harvesting to ginning, cleaning, and spinning to the final stages of manufacturing and distribution, each step plays a vital role in ensuring that high-quality cotton yarn is produced and made available to those who need it.
Conclusion
Cotton is a versatile and sustainable crop employed for centuries to craft a diverse range of textiles. Transforming cotton fiber into yarn encompasses several crucial steps, each of which plays a role in determining the final product’s strength, durability, and visual quality. From the initial stages of cultivation and harvesting, through processes like ginning, cleaning, carding, combing, spinning, ply, and twisting, to the final steps of dyeing and finishing, every phase of the cotton-to-yarn journey demands a high level of expertise, meticulousness, and a keen eye for detail.
Yarn manufacturing and distribution complete the process, bringing the cotton yarn to market for use in clothing, home goods, and industrial applications. One can appreciate the craftsmanship and commitment invested in each cotton strand, whether in your attire, bedding, or towels, wearing a cotton shirt, resting on cotton sheets, or utilizing cotton towels.
As the textile industry continues to evolve, cotton will remain a staple of fabric production, cherished for its softness, breathability, and adaptability. So, the next time you see a garment or household item made of cotton, take a moment to appreciate the journey of how cotton is made into yarn and the skilled artisans who make it possible.
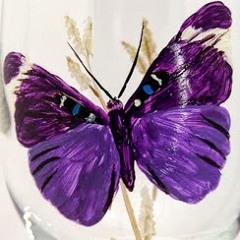
Vera Mondragon, a luminary in the yarn industry, weaves together her passion and expertise. With a knack for creativity and a love for all things yarn, Vera guides enthusiasts through the vibrant world of fibers, offering insights and inspiration for every crafting journey.