Discover How Jute is Processed into Yarn for Crafting
If you’re a crafting enthusiast, chances are you’ve come across jute yarn. It’s a popular natural fiber commonly used in various craft projects, from macramé to crochet. But have you ever wondered how jute is processed into yarn? This article will examine jute yarn production, from harvesting to the finished product.
Jute is a versatile, renewable fiber primarily grown in India, Bangladesh, and Southeast Asia. It’s known for its durability, strength, and natural golden color.
Unravel the journey of jute as it transforms into crafting yarn, and delve into the intricate process of turning cotton into versatile yarn.
Key Takeaways:
- Jute is a popular natural fiber used in a variety of craft projects.
- Jute is primarily grown in India, Bangladesh, and Southeast Asia.
- Jute is known for its durability, strength, and natural golden color.
Understanding Jute Fiber
Jute fiber is known for its strength, durability, and versatility. Cotton has widespread application in manufacturing diverse products, encompassing textiles, paper, and construction materials. However, before the jute fiber can be utilized in various industries, it must first be converted into yarn through a series of processing techniques.
The transformation of jute fiber into yarn involves a series of essential steps, each playing a pivotal role in producing top-notch yarn. The jute processing techniques used in this process include harvesting and retting, breaking and scutching, carding and combing, spinning, and applying twist to the yarn.
Harvesting and Retting Jute
The first step in processing jute fiber into yarn is harvesting and retting. The jute plants are harvested by hand or using a mechanical harvester, and then the stalks are soaked in water to loosen the fibers from the stem. This is known as the retting process in standing water or dew moisture.
During the retting process, bacteria and fungi ferment the pectin that binds the fiber to the stem, separating the fiber from the rest of the plant. After retting, the jute stalks are left to dry in the sun before being transported to the next stage.
Breaking and Scutching
The second step in processing jute fiber to yarn is breaking and scutching. The jute fibers are separated from unwanted impurities such as bark and other plant materials during this stage.
The breaking process involves breaking the jute stalks into smaller pieces, which are then fed through a scutching machine to remove the impurities. The scutching machine is a large, rotating drum with metal blades that beat and separate the fibers.
Carding and Combing
After the breaking and scutching, the jute fibers are carded and combed to align the fibers and remove any remaining impurities. The carding and combing process involves using machines to straighten and organize the fibers, creating a uniform texture that is easier to spin into yarn.
Spinning the Jute Fiber
Once the jute fibers have been carded and combed, they are ready for spinning. In the spinning stage, the fibers undergo twisting and are transformed into yarn using a spinning wheel or a spinning frame. The finished yarn is wound onto bobbins or cones for the next stage of the process.
The final steps in jute yarn production involve:
- Applying a twist to the yarn.
- Winding it onto spools.
- Finishing it for use in crafting or textile production.
Understanding the jute processing techniques involved in converting jute fiber into yarn is essential for creating quality yarn that can be used in various industries.
Harvesting and Retting Jute
Jute is generally harvested between June and September, depending on the geographical location and climate. When the plants reach maturity, they are cut from the stem close to the ground using a sickle or a knife. The stalks are then bundled and left in the field to dry for about a week.
Next, the jute is subjected to retting, which separates the fiber from the stalk. Retting is achieved by either a natural process of microbial action or a controlled process using chemical retting agents. During natural retting, the jute is submerged in water for a few days, and bacteria and fungi break down the pectin and lignin in the stalk, making it easier to extract the fibers. This process takes around two to three weeks and results in higher-quality fibers. In comparison, chemical retting takes only a few days, but the resulting fibers are lower quality.
After retting, the jute is left to dry in the sun for several days. The stalks are then beaten with wooden mallets to separate the fibers from the non-fibrous material. This process is known as breaking. The stalks are then further processed through a scutching machine, which removes any remaining impurities and separates the long and short fibers. The separated fibers are then bundled together for carding.
Conclusion
Harvesting, retting, breaking, and scutching jute requires precision and expertise. Jute processing techniques have evolved, creating more efficient and environmentally friendly methods to produce quality fibers. Understanding the process is fundamental in creating superior quality yarn, and the industry continues to innovate to produce the best materials for the world to enjoy.
Breaking and Scutching: Essential Jute Processing Techniques
After the retting technique separates jute fibers from the plant, the next step is breaking and scutching. This process is crucial in removing unwanted impurities and separating the fibers further.
Breaking is the first step, where the jute fibers are fed through rollers that break them into smaller pieces. The broken fibers are then fed through a scutcher, essentially a machine that separates the fibers from unwanted particles. The scutcher uses rotating wooden blades that beat and remove any residual pith, seed particles, or dust from the fibers. As the fibers pass through the scutcher, they are straightened, making them easier to work with.
Smoothing With a Padder
Once the jute fibers have been scutched, they are fed through a padder. The padder consists of rollers that compress the fibers and smooth them out. This process removes any remaining impurities and aligns the fibers for the following processing stage.
Breaking and scutching are the most crucial steps in jute processing techniques as they ensure the yarn produced is high quality. The process removes any unwanted material, separates the fibers, and prepares them for spinning, where the fibers are twisted and spun into yarn.
Carding and Combing: Aligning and Cleaning Jute Fibers
After breaking and scutching, the jute fibers are carded and combed to remove any remaining impurities and align the fibers. Carding involves running the fibers through a machine with wire brushes that separate and straighten them into a thin web.
The combed fibers are further straightened and aligned by a combing machine, resulting in a smooth, soft yarn with a consistent texture. This process helps to eliminate any unevenness in the fiber, which can affect the quality of the final product.
Jute processing techniques have evolved, and now technology has enabled the automation of these processes, resulting in a more efficient and automated carding and combing process. Modern machinery has also made it possible to produce a broader range of jute yarns with varying thicknesses and quality.
The jute yarn’s quality heavily depends on the carding and combing process. The fibers are evenly aligned using the proper jute processing techniques, producing a high-quality yarn with uniform strength and texture.
Spinning the Jute Fiber
After the breaking and scutching process, the jute fibers are now ready for spinning. This process involves twisting and spinning the fibers into yarn.
The first step in the spinning process is drawing the fibers out into a uniform size and thickness. This is accomplished using a machine called a drawing frame. The drawing frame pulls the fibers out and straightens them, aligning them in parallel.
Next, the fibers are fed into a spinning machine. Spinning involves twisting the fibers to create a robust and durable yarn. The number of twists per inch determines the thickness of the yarn. After spinning, the yarn is wound onto bobbins or cones for further processing.
The final step in the spinning process is winding the yarn onto spools for use in textile production. This is done using a machine called a winding machine. The yarn is wound onto the spools in a consistent and even manner, ready for weaving or knitting.
Overall, spinning is a crucial step in producing high-quality jute yarn. Manufacturers can create a durable and versatile product for various crafts and textiles by carefully aligning and twisting the fibers.
Applying Twist to the Yarn
The next step in the jute yarn production process is applying twist to the fibers to strengthen and stabilize the yarn. The amount of twist applied depends on the desired thickness and strength of the yarn. Generally, the finer the yarn, the more twist is required to strengthen it.
The twist is applied using a spinning wheel or a twister machine. The jute fibers are fed into the machine and twisted together to form a continuous strand of yarn. Subsequently, the yarn is wound onto a bobbin or spool in readiness for subsequent processing.
The twist is critical to the quality of the yarn. Too much twist can cause the yarn to become brittle and prone to breaking, while too little twist can result in a weak and fluffy yarn. Experienced spinners carefully monitor the twist to ensure the yarn has the desired strength and durability.
Winding and Finishing
Once the jute fibers have been spun into yarn, they must be wound and finished before use in crafting. The winding process involves transferring the yarn from the spinning bobbin onto a giant cone or spool for easier handling during weaving or knitting. This can be done manually or by machine, depending on the manufacturer’s preferences and production volume.
After winding, the jute yarn may require finishing processes to improve its appearance and durability. Finishing techniques such as singeing, mercerizing, and dyeing can be applied to the yarn to add strength, shine, and color consistency. Singeing involves passing the yarn over an open flame to burn off any protruding fibers, while mercerizing is a chemical treatment that enhances the yarn’s luster and strength.
Jute Yarn Manufacturing Methods | Jute Yarn Production Process |
---|---|
Winding | I am transferring the jute yarn onto a giant cone or spool for easier handling. |
Singeing | Bringing off protruding fibers with an open flame improves the yarn’s appearance. |
Mercerizing | Chemical treatment to enhance the yarn’s luster and strength. |
Dyeing | Application of color to the yarn for consistency and customization. |
These winding and finishing processes prepare jute yarn for various crafts and textile production. The finished yarn can be woven into carpets, rugs, and mats or used to make bags, baskets, and other decorative items. Given the rising demand for sustainable and environmentally friendly fibers, jute yarn has gained popularity among crafters and manufacturers seeking natural, biodegradable alternatives to synthetic materials.
Utilizing Jute Yarn in Crafts
Jute yarn is a versatile material commonly used in crafting and textile production. With its natural, rustic texture, jute yarn adds a unique touch to any project. Here are some ways to utilize jute yarn in your crafting:
Macramé
Jute yarn is often used in macramé projects such as wall hangings, plant hangers, and jewelry. Its strength and durability make it ideal for creating intricate knot patterns.
Crochet and Knitting
Jute yarn can also be used in crochet and knitting projects, adding a natural look and feel to items such as bags, baskets, and rugs. Its texture and sturdiness make it an excellent choice for functional items that need to hold their shape.
Embroidery and Weaving
Jute yarn can be used in embroidery and weaving to add texture and dimension to designs. Its natural essence produces a distinctive juxtaposition when paired with materials like cotton or wool.
Aside from crafting, jute yarn is also widely used in textile production, particularly in creating rugs, mats, and other home decor items. With its eco-friendly and sustainable properties, jute yarn is popular for those seeking environmentally responsible materials.
Now that you know how versatile jute yarn can be consider incorporating it into your next crafting project or textile production. Its natural texture and durability make it a perfect addition to any design.
Innovations in Jute Yarn Production
The jute processing industry has been around for centuries, and the techniques used in converting jute fibers into yarn have remained relatively unchanged. However, with the advancement of technology and the need for more sustainable manufacturing processes, the industry has seen several innovations in recent years.
One such innovation is using more eco-friendly methods for retting jute fibers. Traditionally, jute fibers were retted by soaking them in water for a few days, which wastes considerable water and causes pollution. However, new techniques involve retting the fibers using microbial processes, significantly reducing water consumption and pollution.
Another development in the jute processing industry is the introduction of automated machinery for the spinning process. Manual spinning processes are time-consuming and labor-intensive, making them expensive and unsustainable. Automated spinning machines are faster, more efficient, and require less labor, making them a more sustainable option.
Moreover, endeavors are underway to innovate techniques for manufacturing finer jute yarn. Traditionally, jute yarn was coarse and used mainly for heavy-duty applications. Still, with innovations such as micronaire-controlled carding machines, finer and more delicate jute yarn can be produced for various products such as clothing and home furnishings.
The jute processing industry continues to evolve, driven by the need for more environmentally friendly and sustainable manufacturing processes. These innovations will ensure that jute remains a valuable and versatile material in textiles and crafts.
Conclusion
In conclusion, understanding the jute processing techniques is crucial for creating quality jute yarn. Converting jute fibers into yarn for crafting involves several steps, including harvesting and retting, breaking and scutching, carding and combing, spinning, applying twists, and winding and finishing.
It is important to note that recent innovations in the jute processing industry may affect the production of jute yarn and other jute-based products. Keeping up-to-date with these innovations can help manufacturers improve their processes and produce better-quality products.
Jute is a versatile and sustainable material used for centuries in various textile industries. By understanding the jute processing techniques, manufacturers can continue to produce quality jute yarn for use in different crafting projects and textile production.
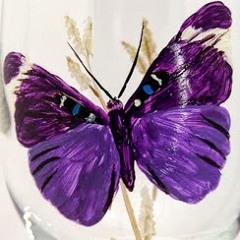
Vera Mondragon, a luminary in the yarn industry, weaves together her passion and expertise. With a knack for creativity and a love for all things yarn, Vera guides enthusiasts through the vibrant world of fibers, offering insights and inspiration for every crafting journey.